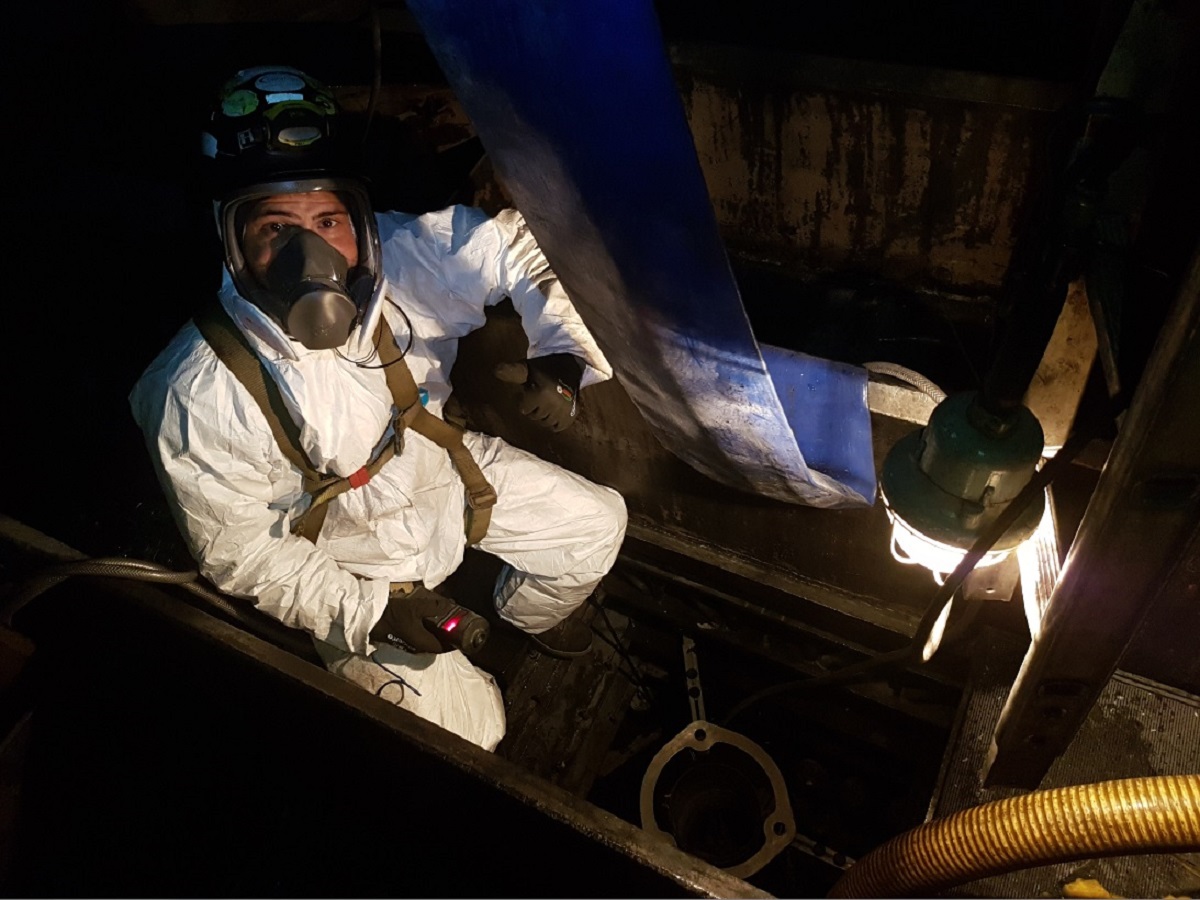
Publié par CREALYST le 10/12/2018
LA MANIPULATION DES CATALYSEURS : UNE QUESTION DE SÉCURITÉ ET DE PERFORMANCE DES PROCÉDÉS
« Focus on Crealyst dense loading experience »
Article publié dans la revue IFP school Alumni Mag N°268- Mars 2018
The economic environment of the refining industry is, by nature, very competitive. As a result, refiners have always paid a lot of attention to the performance of their process units, the challenge of the energy transition making this objective even more critical.
Most process units are using costly sophisticated catalysts aimed at improving performance. However, selecting the best catalysts may be meaningless if they are not correctly used which, in the case of fixed bed reactors, implies a perfect and safe loading.
It is widely recognized that efficient catalyst loading significantly increases process unit’s performance by improving the flow distribution inside the reactor, here meaning the contact between solid (i.e. the catalyst), liquid and gas. This also prevents any settling of the bed and results in more reliable operations.
Dense loading may allow either to increase the unit’s throughput by about 10% at a constant reactor inlet temperature or to achieve the same performance level at a lower operating temperature, allowing reduced fuel consumption.
Crealyst proposes an attractive option to the refiners by offering its patented HDL Process® which provides dense loading of catalysts using the Calydens® Equipment.
Based on extensive proven know-how from highly qualified specialists, this technology allows for the reduction of the void volume within the catalyst pellets to its very minimum and gives a homogeneous fixed bed with a packed density increased by around 20% compared to conventional loading.
The Crealyst approach is also aimed at ensuring the maximum safety level. This is achieved thanks to a dedicated training of operators allowing them to work inside reactors in complete safety (see box). Moreover, due to its light weight (15 kgs), the Calydens device can be easily and quickly installed, resulting in less time spent by the operator inside the reactor. And thanks to the use of soft brushes, the catalyst distribution system produces less dust, for the benefit of operator’s health.
Crealyst has realized dense loading in more than 1,700 reactors or adsorbers for a total cumulated amount of 150,000 metric tons of alumina or zeolite based catalysts and molecular sieves.
Catalyst loading under inert atmosphere: a critical safety issue
Some catalysts must not be put in contact with oxygen or water to avoid ignition or loss of performances. So, they need to be handled under nitrogen atmosphere.
During loading or unloading of such catalysts, operators may have to enter the reactor and work under inert atmosphere. Such operations are very critical with regard to safety and require taking rigorous precautionary measures to avoid asphyxia.
Appropriate equipment, procedures and training are required to ensure that breathable air is always provided to the worker and that he can escape safely should an unforeseen problem occur.
For that purpose, Crealyst ‘s dense loading specialists benefit from a full week intensive dedicated training program set up by INPP in its Marseille facilities (see picture).